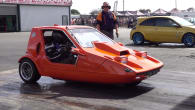
With a turbo Hayabusa engine, this is the Bond Bug from hell
Three wheels plus a turbocharged Hayabusa engine equals the world's quickest death trap.
Browse over 9,000 car reviews
The heart of most vehicles today, the internal combustion engine has advanced significantly over its century long history.
This series outlines some of the key innovations in engine technology before taking a look at alternatives to the combustion engine. This week, turbocharging.
Check out the other parts in this series
Tech through time: Fuel injection
Tech through time: Supercharging
Tech through time: Variable Valve Timing
Tech through time: Hydrogen Fuel Cells
The concept of a turbocharger to generate extra power was first patented by Swiss engineer Alfred Büchi in 1905, and was subsequently used in several aircraft engines during the early 20th century. In 1962, General Motors became the first manufacturer to utilise a turbo engine in a mass-produced vehicle with the Oldsmobile Cutlass Turbo Jetfire.
Like supercharging, turbocharging is another method of developing more power from an engine without increasing displacement. The key difference between the two technologies is how they are powered. Whilst a supercharger is mechanically driven via a belt that connects it to the engine’s crankshaft, a turbocharger is powered by the exhaust gases from the engine.
These exhaust gases, in turn, spin a turbine up to 150,000 RPM. The turbine is directly connected via a metal rod to the compressor, which compresses the air, thus allowing a greater volume of air to enter into the combustion chamber, more fuel to be mixed and consequently more power to be generated.
The intercooler (more precisely known as the charge air cooler) is another key part of a turbocharged engine. When air is squeezed by the compressor, it becomes warm and therefore less dense. The intercooler, typically an air-to-air intercooler, passes the compressed air through a series of cooling fins. Cooler air from outside mingles with this compressed air and draws heat away. Thus, the intercooler makes the turbocharging process more efficient by ensuring that only cool air enters the combustion chamber.
A key problem with a turbo car is lag. Unlike a supercharger, the performance of a turbocharger is dependent on the amount of exhaust gas produced by the engine. At a low RPM, the engine produces less exhaust gas. The exhaust turbine doesn’t spin very fast, the compressor cannot compress much air, and therefore the turbocharger can’t provide much boost. When you push the accelerator pedal in an ordinary turbocharged car, there is a noticeable ‘lag’ as the engine builds up enough revs and exhaust gas to power the turbo and thus provide boost.
Thus, one of the key dilemmas that car manufacturers face with turbocharging is how to alleviate lag, whilst also providing a consistent amount of boost regardless of engine RPM.
One option is to include a sequential system with a small turbocharger operating at low RPMs, and a larger turbo operating at higher RPMs, similar in principle to including both a small and large windmill. The smaller windmill will be easier to spin when the airflow is low, and the larger windmill can take over when the airflow is high to generate more boost.
Another option is to use a turbo that can regulate the speed of the exhaust gas entering the turbine, to ensure it quickly spools up and provides a consistent level of boost across the engine’s RPM range.   Â
This is known as a variable geometry turbocharger. In principle, this is similar to using a windmill that could change its size to produce a consistent level power depending on how much air was passing through it.
A variable geometry turbo works by using several vanes placed around the exhaust turbine. These vanes pivot in response to the airflow coming into the turbo. When there is a reduced exhaust gas airflow at a low engine RPM, the vanes adopt a more narrow, ‘closed’ position that squeezes the air at a high velocity into the turbine, allowing it to spool up and spin more quickly. At a high engine RPM there is a greater exhaust gas airflow and the gas doesn’t need to be sped up. Therefore, the vanes open up, thus ensuring the turbine spins at the same rate.
The cylinders in a combustion engine do not all fire at the same time. Instead, they use a sequential firing order, such as 1-3-4-2 for a four cylinder engine. A twin scroll turbo utilises this basic principle to achieve the same objective as a variable geometry turbocharger.
Based on their firing order, cylinders are paired into two different channels (‘scrolls’). Instead of pivoting vanes, these channels are differently sized. One channel, for example, is smaller than the other to increase the speed of the exhaust gas airflow at a low engine RPM, whilst the larger channel allows the greater volume of exhaust gas generated at high engine RPMs to efficiently flow into the turbine. The channels may also be positioned to direct air at different parts of the turbine blades to further increase efficiency. Thus, these channels effectively control the airflow into the turbine to reduce lag and also improve the level of boost provided at higher engine RPMs.
Today, turbochargers are a mainstream option used across the entire automotive industry. Budget vehicles such as the Skoda Fabia, and hypercars such as the Bugatti Chiron all utilise the same fundamental principle to improve engine power. Despite the advent of variable geometry and twin-scroll turbos, the problem of turbo lag has not been eliminated completely.
Electric turbos are one solution that eliminates this lag entirely. The Audi SQ7, the world’s first production vehicle to incorporate this technology, utilises an electrically powered compressor in conjunction with two sequential turbochargers. Being electrically powered, the compressor can run from 0 RPM without the need for exhaust gas, providing instant boost before the conventional turbos take over at higher RPMs. Whilst limited in use now, this type of technology is likely to become more prevalent in turbocharged cars in the near future.
Are you a turbo trooper or is it NA all day? Tell us what you think in the comments.
Three wheels plus a turbocharged Hayabusa engine equals the world's quickest death trap.
What better place to showcase the future of electric Russian cars than a military expo?
Comments