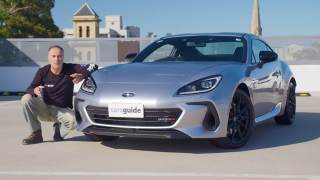
Lightweight revolution
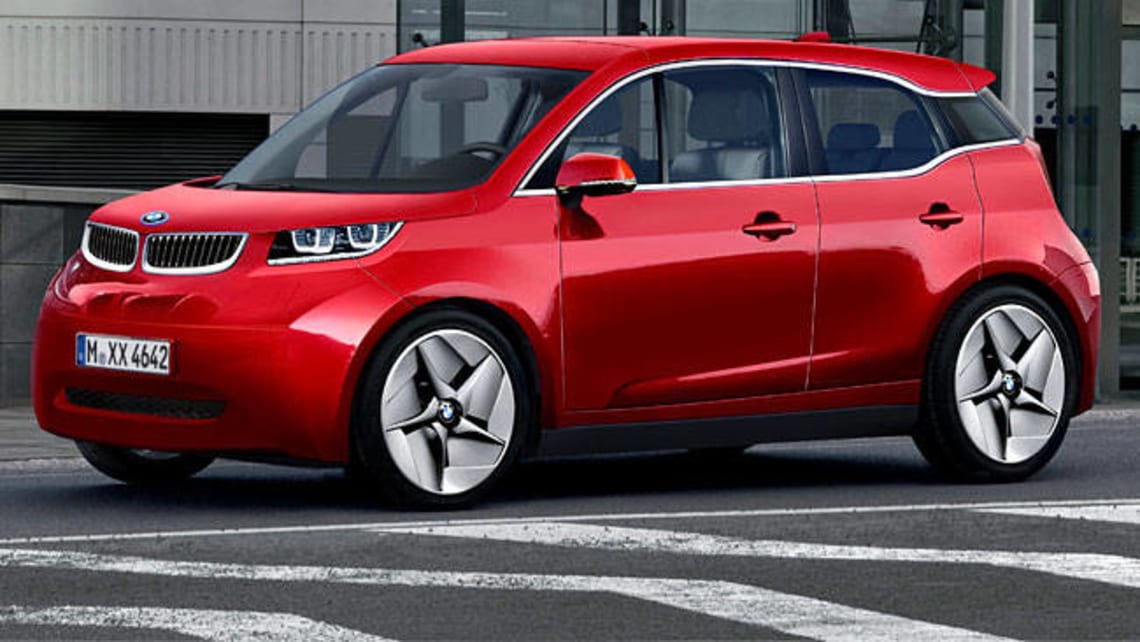
…..they were once reserved for F1 cars, MotoGP bikes and aeroplanes.
Carbon fibre-reinforced plastic (CFRP) is the starting block for just about every new vehicle on the drawing board. Depending on the weave, curing process and resins used to bond the composite material, it can be used to create decorative interior components or durable parts of the vehicle body.
This hi-tech material is already used in the Lamborghini Aventador’s monocoque cockpit and for 65 per cent of the Lexus LF-A body, but the BMW MegaCity Vehicle (also known as the i3) will be the first mass-produced car to use a CFRP passenger cell when it goes on sale in 2013.
CFRP is at least half the weight and has similar or better crash integrity to a comparable steel structure. One of the problems in applying CFRP to mass-production has been the cost of the process – components are cured using extreme heat and pressure – but BMW says its i3 uses a low-cost process that will keep the price to less than $45,000 a car.
The Australian-built FR-1 concept car that wowed visitors to Melbourne’s last International Motor Show is another vehicle to use carbon fibre. Auto Horizons Foundation head Brian Tanti conceived the project as a showcase of what local talent can achieve.
Tanti says the project team’s work with Boeing – a global leader in CFRP research – and the Victorian Centre of Advanced Materials and Manufacturing has given local auto students a leg-up in dealing with emerging technologies.
"It’s not just the carbon-fibre layering process, it’s the whole application of thinking outside the square, in this case to create low-cost solutions to what has traditionally been an expensive process," Tanti says.
"As an auto nation we’re too small to export global volumes of hardware, but if we get the training right we can export talent."
Comments